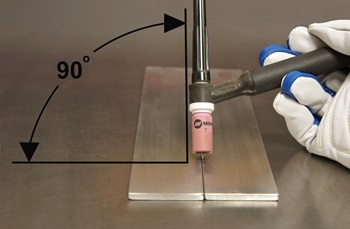
Next a ceiling-mounted pipe that has to be welded from the inside. For pipe welding however a particularly compact torch is required ideally one that is small and flexible with a short torch.
The first is the work angle which is the relationship between the joint and the torch or rod.
Tig welding torch angle. Angle of the Dangle. Resolving welding issues with torch angle adjustment 1. The torch angle relative to the direction of the weld.
If TIG welding particularly noticeable in aluminum a steep. The angle relative to the sides of the weld should be monitored as well. This second plane is.
Perhaps the most important skill needed for TIG welding is moving the torch in a controlled manner with steady forward movement while keeping the gap between the tip of the electrode and the base metal consistently small usually in the range of 18 inch to 316 inch. It requires a lot of practice to precisely control the arc length keeping it as short as you can without allowing the electrode to. Above all it shows what a delicate process TIG is.
The torch movement is steady in the video and briefly stops while the filler material is added. The torch is held at about 20 degrees from vertical tilted so the tungsten points in the direction of the weld. For more tig welding tipskeep scrolling.
TIG Torch angle should only be around 10 degrees or less. Ideally torch angle should only be around 15 degrees or less. Too much torch angle will deflect the heat and melt the rod before you ever get it into the puddle.
Tig Welding Penetration Tungsten Electrode Grind Angle - YouTube. Mightytower41a h en 30. What torch angle to hold during TIG Welding Aluminum.
You should maintain a torch angle of about 15 degrees during TIG Welding Aluminum. This torch angle has two benefits. Firstly it does not block your view on what is going on at the puddle.
Angle There are two torch angles to remember when welding. The first is the work angle which is the relationship between the joint and the torch or rod. Ideally youll hold your torch perpendicular or 90 degrees to the joint.
The big exception to the rule is T-joints where the work angle varies between 30 to 50 degrees. The second angle used in welding is the travel angle. A swivel head torch can help in the front-back direction but if youre welding in the usual sense of Left-right many times torch angle is simply because we need to see the puddle and its right under the tungsten so angle-ing the torch just slightly off to the side is usually necessary.
HTP Invertig 400 ACDC HTP Invertig 221 DV. Thats why the torch bodies and caps come in different lengths with varying torch angles and even flexible torch bodies that can be bent to shape. First a fillet weld on the workbench.
Next a ceiling-mounted pipe that has to be welded from the inside. The work on the welding table can be done using practically any torch body. For pipe welding however a particularly compact torch is required ideally one that is small and flexible with a short torch.
For uphill mig a 90 degree angle works good. So does a slight push angle of up to about 10 degrees. For downhill mig a 90 degree works but a pull torch angle of up to 20 deg seems to work better at keeping the puddle pushed back from the arc.
The work angle for the torch is either a 60-70 degree drag angle or else a 10-20-degree work angle. You must point the electrode along the horizontal edge to weld instead of the vertical edge. You may strike the arc now for the formation of the weld puddle.
While TIG Tungsten Inert Gas is one of the most common welding techniques in use today the process of producing clean high-quality welds is not that easy because there are lots of factors consider from the heat control the technique being used down to the skill of the welder. In short TIG welding can be challenging to greenhorn welders. So if you are struggling with proper TIG welding.
98 Sailor Malan Ave Aeroton Johannesburg 2013. 011 434 7000 Whatsapp. 011 434 7000 Email.
TIG Torch WP-17 4M No reviews. WP-17 Tig Torch is an air-cooled lightweight Tig torch with a modern ergonomic handle and swivel joint to allow for easy handling when welding. TIG Welding Techniques.
The angle of the torch should be 15 to 20 degrees away from the direction of travel. This increases visibility of the area and allows easier access for the filler material. The filler metal should be brought in at as low an angle as possible to help avoid touching the tungsten electrode and contaminating it.
This is because the cup of the TIG torch is always leaning on the weld joint and the arc length is kept the same. Arc length is the key when it comes to TIG welding bead appearance. To walk the cup you need to place the TIG torch cup on the weld joint and set the tungsten so that it is just above the weld.
Hold the MIG gun at a 90-degree angle to each piece of metal when welding a butt joint to direct the heat and filler metal equally to each piece of material. Butt weld a 180-degree joint. Hold the gun at a 90-degree angle to the workpiece directing the filler metal straight into the joint but dont forget to include your travel angle of 5 to 15 degrees.
With TIG welders dragging the tungsten rather than pushing it makes the weld susceptible to the Venturi effect and can increase the porosity of the joint. This leads to an ugly and unstable braze or weld. Instead the welder should push the TIG torch forward at a very slight angle 10-15 degrees vertical angle.
The torch also possesses an ergonomic handle giving you ability you to move it at a 360-degree angle and use on any welding projects you want even tight spaces. Weldtec Speedway SW-320SA-25DX Deluxe TIG Torch Kit Speed Angle 25 Braided Modern flexible over braided rubber hoses and power cables provide flexibility and maneuverability.