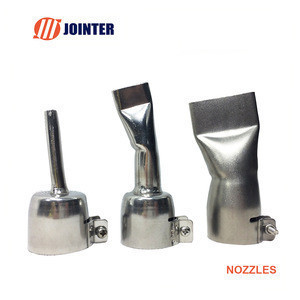
The strength of the joint exceeds that of soldering and no cleanup is required. The flat tip creates a larger weld and can be used when appearance is less important.
Do not weld on containers that have held combustibles or on.
Spot welding stainless steel tips. Cleaning and preparing the stainless steel is the key for proper welding. Because the metal has a strong affiliation to the carbon steel. Keep the toolset separate to clean the stainless steel before welding.
Any tool with residual carbon may contaminate the stainless steel and leads your final product to. Spot welding of stainless steels is usually carried out on thin sheets. Thats not to say that you cant weld stainless with rocker type welders its just that it will be harder to set up and difficult to obtain pressure with the longer arms.
This means excess splash when welding. Always read and follow the safety precautions and operational instructions in your owners manual. Resistance welding is not recommended for aluminum copper or copper alloys.
Use for steel and stainless steel only. For more heat amperage output use shorter tongs. Suppliers of RW tips offer other grades developed specifically for welding galvanized steel stainless steels and aluminum- and nickel-based alloys.
Most often metal formers will want to use an RW electrode with a straight pointed-nose tip and a 14-in-dia. Standard spot welding tip shape have dome tip pointed tip flat tipcone tipradius tipeccentic tip and offset cap tip nosesIf you need special shape of welding tipwe can customize according to your tips drawingThey are popularly used to weld stainless steel platehigh carbon hot form steel platelow carbon steel sheet plategalvanized steel sheet etcIn order to produce high quality spot welder. Always Clean Stainless Surfaces Prior to Welding Stainless steel is subject to contamination by high-carbon steels and other metals.
When this happens it significantly reduces the corrosion resistance of the stainless. Cleaning the surface of your stainless not only helps to reduce contamination risks but will strengthen the weld. The flat tip creates a larger weld and can be used when appearance is less important.
The shank is tapered for easy press-fit installation. Spot Welding Electrodes with Pointed Tip The pointed tip is best for tight areas or for a small weld. Do not spot weld where flying sparks can strike flammable material.
Protect yourself and others from flying sparks and hot metal. Be alert that welding sparks can easily go through small cracks and openings to adjacent areas. Watch for fire and keep a fire extinguisher nearby.
Do not weld on containers that have held combustibles or on. A show machine automatically assembles tie tacks using butt welding to join a sharp steel pin to the back of a dime. The actual time required to weld the pin is about 50 milliseconds and no marking or discoloration occurs on the front of the dime.
The strength of the joint exceeds that of soldering and no cleanup is required. When spot welding zinc coated steels electrodes must either be frequently exchanged or the electrode tip surface should be dressed where a cutter removes contaminated material to expose a clean copper surface and reshapes the electrode. Pro Tip for Best Practices.
One way to prevent warping when welding stainless-steel is to clamp a piece of brass or copper behind the seam of the weld. This will serve as a cooling mechanism or heat sink absorbing the heat while preventing any burn through. It could also help you weld the entire seam continuously.
The TITE-SPOT Pliers has the welding tips sharpened to 316 diameter when new. The tips can be allowed to fatten to 14 diameter before they need to. The spot-weld time interval is so short that the stainless does not have adequate time to start making the transformation.
Metallographic studies and salt-spray testing have never revealed any sensitization or short coming in the corrosion resistance of our spot welded stainless steel assemblies. In some spot welding studies using austenitic 304 stainless steel it has been reported that weld core diameter and weld tensile strength increase up to a certain optimum value due to increased. Jeff explains spot welding and gives a short demo welding stainless steel sheetDarkmoon Metals is a home based business start up I have deci.
Spot welding is widely used in welding carbon steel because they have higher electrical resistance and lower thermal conductivity than the electrode that made from copper. The Spot welding is commonly being used in automobile industry where it is used to weld the sheet metal forming a car. Spot welders can also be completely.
Spot Welding 22 gauge sheet steel - YouTube. It is highly important to clean the metal before any type of welding and cleaning helps get rid of all the dust and other particles before welding stainless steel. And one thing to remember is that you should refrain from using the same brush that is used for cleaning carbon steel because the residue carbon left in the brush can get embedded over the stainless steel and starts rusting it in no time.